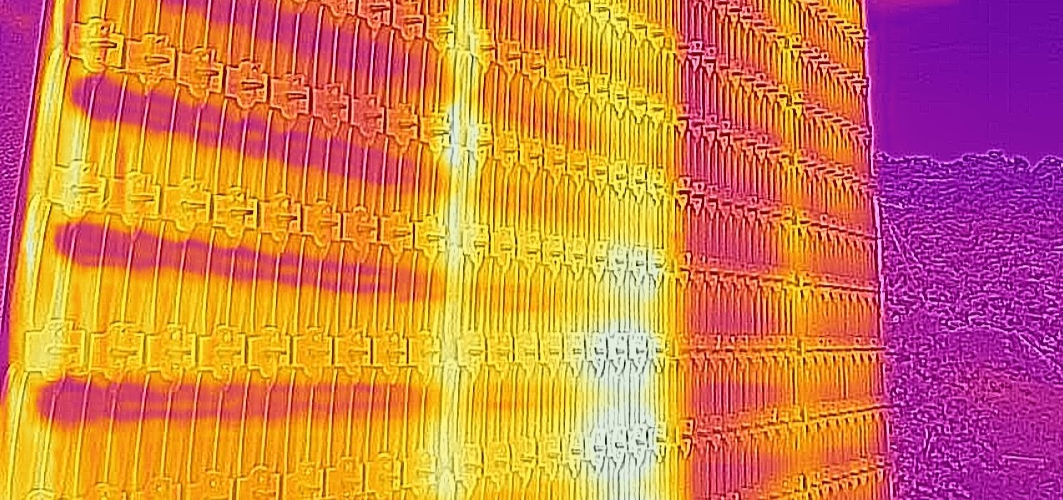
Specialize in customized solutions
Luehr Gas-Cooler (Gas to Air)
This robust technology, often combined with the Luehr Filter Air Pollution Control technology, offers a wide range of advantages for footprint, consistent cooling performance, and corrosion resistance together with an on-line cleaning system for the cooling tubes.

Luehr Gas-Cooler (Gas to Air)
The Luehr Filter process gas cooling solutions from Kuttner North America offer proven performance in dirty gas applications across numerous industries around the world. This robust technology, often combined with the Luehr Filter Air Pollution Control technology, offers a wide range of advantages for footprint, consistent cooling performance, and corrosion resistance together with an on-line cleaning system for the cooling tubes.
Featuring the patented Luehr Filter "Flat Tube" Gas-Cooler
Kuttner’s system provides:
-
A compact & modular design—requiring less physical space than conventional gas coolers, with greater effective cooling surface area.
-
These modular gas coolers can be configured with multiple cooling passes through a single housing which reduces the overall system size.
-
Clean cooling air passes through the inside of the “flat” cooling tubes. This eliminates the tedious, 1 by 1, clean out for the interior of the tubes.
-
A continuous, on-line, mechanical cleaning system is included to prevent the dust buildup on the exterior walls of the flat tubes.

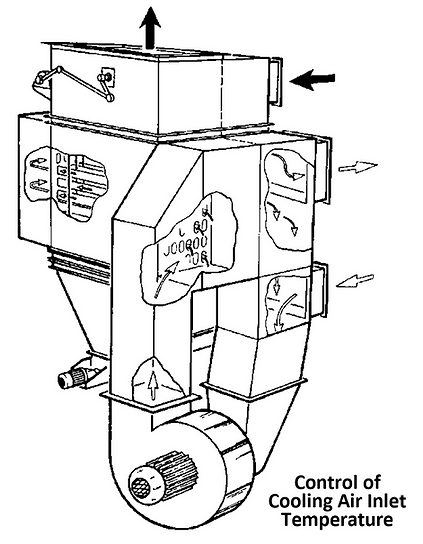
-
Preventing the dust buildup on the outside of the cooling tubes allows for consistent and controllable cooling performance over long operating campaigns, even in high dust processes or applications in which the dust has strong adhesive properties.
-
A packaged cooling air recirculation system preheats the cooling air to avoid operation at temperatures approaching, or below, dew point.
-
The preheated cooling air provides a strong defense against cold end corrosion of the cooling tubes and allows for the substitution of less costly materials for the tube construction.
-
Heat exchanger housing and tube design are such that individual tubes can be exchanged so that replacement of a complete tube bundle is not necessary.
-
Re-use of cooling air is possible for facility heating or generation of hot water.
The exceptional process gas cooling system from Luehr and Kuttner North America offers unique, patented features for efficient, reliable performance.
Here’s how it works…
-
The clean, ambient air (or filtered process gas) is blown through the inside of the flat cooling tubes via the cooling air fans.
-
If cooling air preheating is necessary (as a measure to prevent corrosion), one or more VFD controlled, centrifugal fans force the cooling air through the flat tubes. Once the cooling air has passed through the tubes, a portion of the now warm air is mixed with the fresh ambient air to control the inlet temperature of the cooling air at a level safely above dew point.

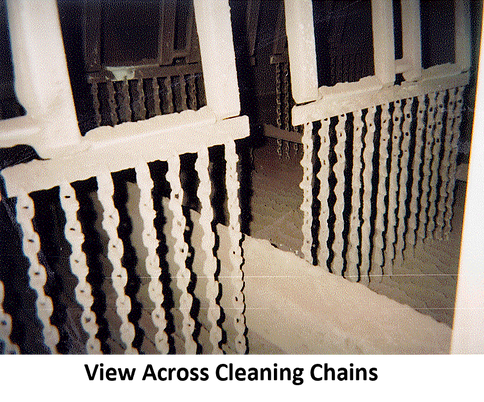
-
If preheating of the cooling air is not required (i.e., exhaust gases are not corrosive), a series of axial cooling air fans are integrated into the housing doors of the cooler.
-
For all gas coolers, a continuous, on-line cleaning system prevents formation of thick dust layers along the sides of the cooling air flat tubes.
-
The continuous, on-line cleaning system is comprised of a series of oscillating chain curtains that sweep the dust layer away from the flat walls of the cooling tubes.
-
The dust that is dislodged from the surface of the cooling tubes falls into the dust hopper where it is continuously removed by the dust discharge device (screw conveyor, rotary valve, or dump-valve).