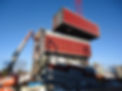
​
​
Focused on customized solutions
Air Pollution Control
Luehr Filter’s Air Pollution Control (APC) technology has been successfully installed for all manner of complex industrial and combustion processes around the globe. Our portfolio of references include hundreds of installations for the ferrous and nonferrous metals industries. This includes melting of iron and steel in the foundry industry (cupola, induction, electric), melting and smelting of non-ferrous metals (aluminum, lead, copper, brass, zinc, etc.), steel mills, and sintering operations, as well as mineral and chemical process. In addition, we have installations at more than 50 waste-to-energy facilities for all types of waste (domestic, municipal, industrial, hospital, hazardous, e-scrap, RDF, sludge, coal, tires, etc.).
These references range from high efficiency particulate control, to state-of-the-art multi-pollutant (PM, PM2.5, SOx, HCl, HF, dioxins & furans, Hg and heavy metals, NOx and odor abatement) with varying types of sorption technologies and techniques in single-stage and multi-stage systems.

PM Removal
Luehr Filter’s patented support cage and flat bag technology provides for a much smaller overall baghouse footprint compared to conventional round-bag filters. This small footprint is particularly beneficial for retrofit and/or baghouse replacement projects at facilities with problematic space constraints.
Luehr Filter’s innovative flat bag technology and patented support cage also provide for exceptionally long filter life. Filter life in the range of 6 to 10 years is common even for difficult combustion processes. This filter life provides a direct reduction for operating costs.
Sorption Technology for Multi-Pollutant Removal
The varying chemisorption / adsorption techniques utilized by Luehr Filter APC systems include the following:
-
Exhaust gas conditioning - tempering and humidity control for optimal sorption conditions.
-
Highly reliable, mechanical recirculation of the additive materials, with dust recycling rates up to 50 times through the system, resulting in reduced consumption of additives and operation at low stoichiometric ratios.
-
Careful selection of additive materials (calcium or sodium based) based on flue gas conditions, together with local availability of the materials.
-
Improved SO2 reduction with humidifying of the recycled additive materials.
